The Unsung Architects of Industry: A Deep Dive into the World of plant Operators
In the heart of bustling industrial complexes, amidst the hum of machinery and the hiss of steam, a critical role quietly ensures the smooth and efficient operation of vital processes: the plant operator. These individuals, often overlooked, are the backbone of countless industries, from power generation and chemical manufacturing to water treatment and oil refining. Their expertise, vigilance, and problem-solving skills are essential for maintaining safety, productivity, and environmental compliance.
The term “plant operator” encompasses a broad spectrum of responsibilities, varying depending on the specific industry and the complexity of the plant. However, certain core duties remain consistent across the board:
Monitoring and Controlling Processes

Plant operators are the eyes and ears of the plant. They meticulously monitor gauges, meters, and computer screens to track critical parameters such as temperature, pressure, flow rates, and chemical compositions. This constant vigilance allows them to identify deviations from normal operating conditions and take corrective actions before problems escalate.
Operating and Maintaining Equipment
Operators are responsible for starting, stopping, and adjusting equipment such as pumps, valves, compressors, turbines, and reactors. They perform routine maintenance tasks, including lubrication, cleaning, and minor repairs, to ensure equipment reliability and longevity.
Troubleshooting and Problem-Solving
When unexpected issues arise, plant operators are the first line of defense. They use their knowledge of the process and equipment to diagnose problems, implement solutions, and restore normal operations. This often requires quick thinking and the ability to work under pressure.
Ensuring Safety and Compliance
Safety is paramount in any industrial setting. Plant operators adhere to strict safety protocols, including lockout/tagout procedures, confined space entry permits, and emergency response plans. They also ensure compliance with environmental regulations by monitoring emissions and waste streams.
Documenting and Reporting
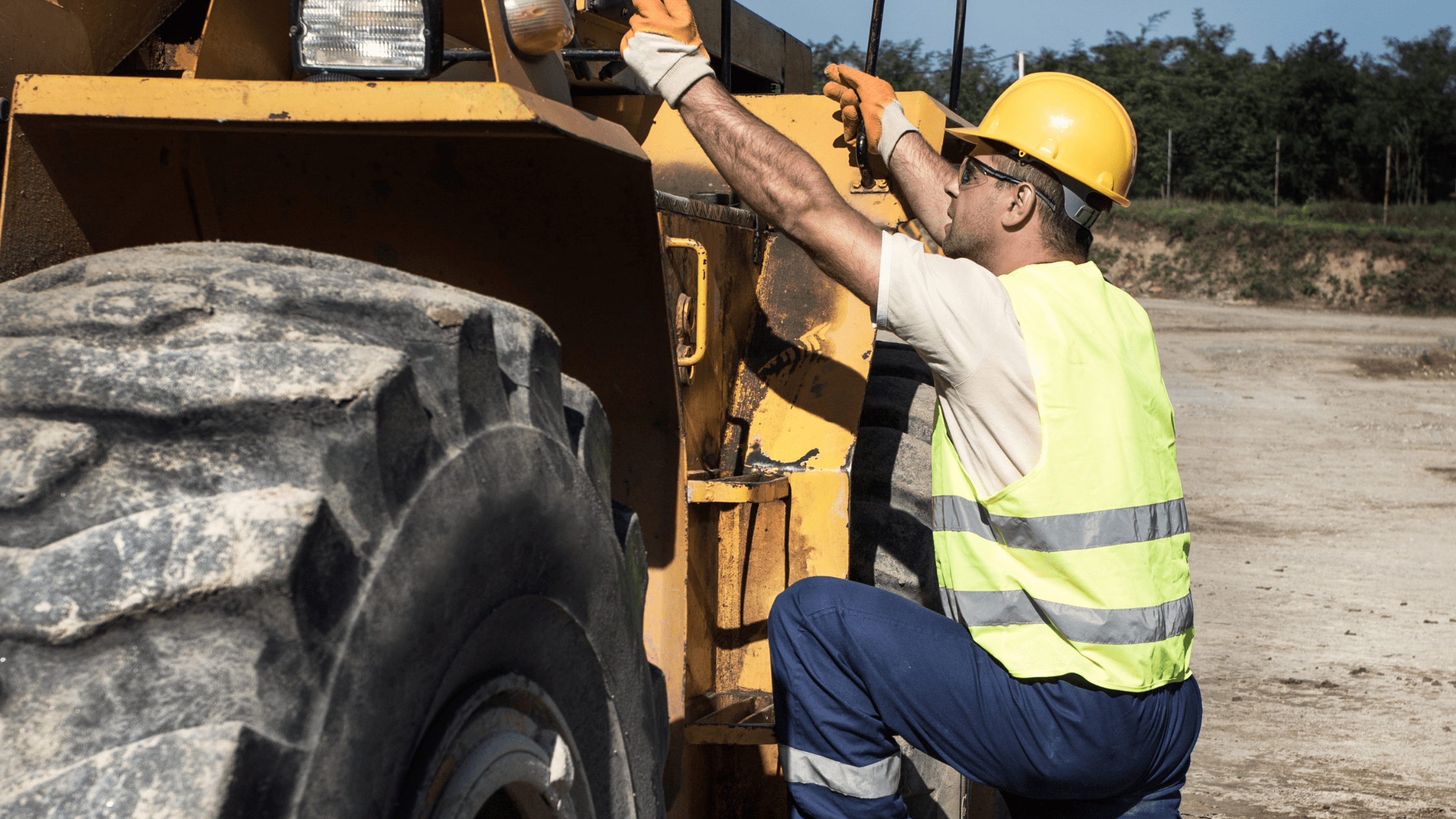
Operators maintain detailed records of plant operations, including process parameters, equipment maintenance, and incident reports. This documentation is crucial for tracking performance, identifying trends, and ensuring regulatory compliance.
Plant operators are integral to a wide range of industries, each with its unique challenges and demands:
Power Generation
Operators in power plants manage the complex processes involved in generating electricity, including controlling boilers, turbines, and generators. They ensure a stable and reliable supply of power to homes and businesses.
Chemical Manufacturing
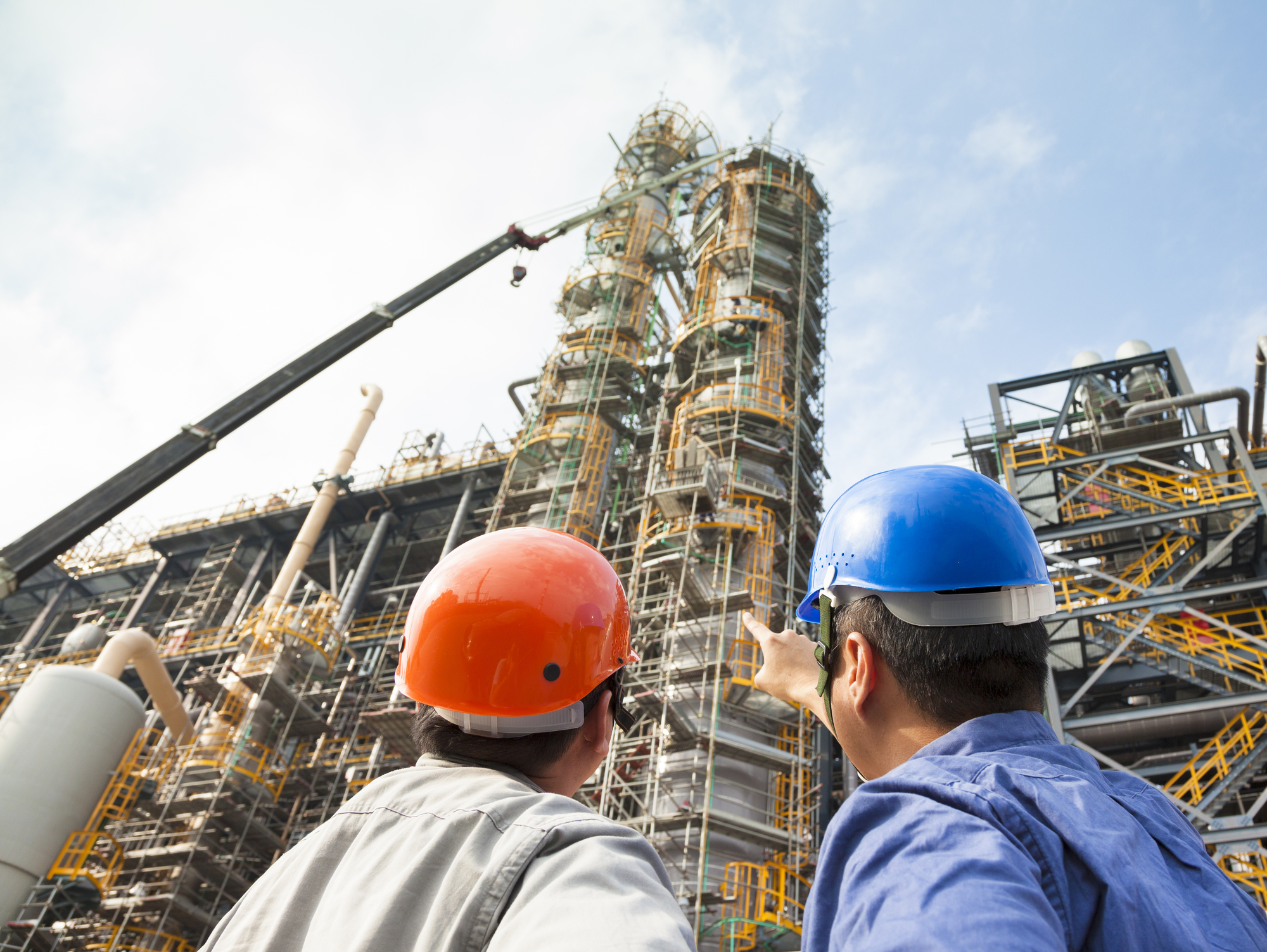
Chemical plant operators control the production of various chemicals, from basic commodities to specialized products. They manage reactions, distillations, and other processes, ensuring product quality and safety.
Oil and Gas Refining
Refinery operators oversee the processing of crude oil into various petroleum products, such as gasoline, diesel, and jet fuel. They manage complex distillation towers, catalytic crackers, and other equipment.
Water and Wastewater Treatment
Operators in water treatment plants ensure the safe and reliable supply of potable water. They control filtration, disinfection, and other processes to remove contaminants and meet water quality standards. Wastewater treatment operators manage the processes that remove pollutants from sewage and industrial wastewater before discharge.
Food and Beverage Processing
Plant operators are employed in food and beverage manufacturing to control the production of various products, including dairy, beverages, and packaged foods. They ensure product quality and safety by managing processes such as mixing, heating, and packaging.
The role of a plant operator demands a unique combination of technical skills, practical experience, and personal attributes:
Technical Knowledge
A solid understanding of the principles of thermodynamics, fluid mechanics, chemistry, and electricity is essential. Operators must be able to interpret process diagrams, equipment manuals, and technical specifications.
Hands-on Experience
Practical experience in operating and maintaining industrial equipment is highly valued. Many operators begin their careers as technicians or mechanics before advancing to operator roles.
Problem-Solving Skills
Operators must be able to identify and troubleshoot problems quickly and effectively. This requires analytical thinking, attention to detail, and the ability to work under pressure.
Communication Skills
Effective communication is crucial for coordinating with other operators, supervisors, and maintenance personnel. Operators must be able to clearly convey information and follow instructions.
Safety Consciousness
A strong commitment to safety is paramount. Operators must be able to follow safety procedures, identify hazards, and take appropriate precautions.
Physical Stamina
Plant operators often work in challenging environments, requiring physical stamina and the ability to stand for long periods, lift heavy objects, and work in confined spaces.
The path to becoming a plant operator can vary depending on the industry and the specific requirements of the employer. However, some common pathways include:
Technical Training
Many community colleges and technical schools offer associate degrees or certificates in process technology or related fields. These programs provide a foundation in the principles of plant operations and equipment maintenance.
Apprenticeships
Apprenticeships offer a combination of classroom instruction and on-the-job training. These programs typically last several years and provide a structured pathway to becoming a skilled plant operator.
Military Experience
Veterans with experience in operating and maintaining military equipment often possess the skills and qualifications required for plant operator roles.
On-the-Job Training
Some employers offer on-the-job training programs for entry-level positions, allowing individuals to gain experience and advance to operator roles.
The field of plant operations is constantly evolving, driven by technological advancements and changing industry demands. Some key trends shaping the future of the profession include:
Automation and Digitalization
The increasing use of automation and digital technologies is transforming plant operations. Operators are now responsible for monitoring and controlling complex systems through computer interfaces and remote monitoring tools.
Data Analytics and Predictive Maintenance
Data analytics is being used to analyze plant performance data and predict equipment failures. This allows operators to proactively address issues and prevent downtime.
Sustainability and Environmental Compliance
The growing emphasis on sustainability and environmental compliance is driving the adoption of cleaner and more efficient technologies. Operators are playing a key role in reducing emissions and minimizing waste.
Cybersecurity
As plants become more interconnected, cybersecurity is becoming a critical concern. Operators must be aware of potential cyber threats and take steps to protect plant systems from attacks.
Plant operators are the unsung heroes of industry, ensuring the safe, efficient, and reliable operation of vital processes. Their expertise, vigilance, and problem-solving skills are essential for maintaining productivity, protecting the environment, and meeting the demands of a modern society. As technology continues to advance and industries evolve, the role of the plant operator will remain critical, adapting to new challenges and opportunities. Their dedication and skill are the foundation upon which countless industries depend.